

Check category

Do you understand the development prospects of precision casting manufacturers?
Investment casting, also known as investment casting, is a precision casting process with very little or no laser cutting. It is a production process in the field of precision casting, and its use is very common. It can not only be used for precision casting of various types and metals, but also produces castings with higher dimensional precision and surface quality than other precision casting methods. Castings that are more complex, heat-resistant, and less prone to production and processing can be used. High precision precision casting.
The true application of contemporary investment casting methods in industrial production was in the 1940s. At that time, the advancement of aviation companies' turbojet engines required the production and manufacturing of wear-resistant alloy steel components, such as leaves, centrifugal impellers, nozzles, etc. They had complex shapes, accurate specifications, and smooth surfaces. Because wear-resistant alloy steel raw materials cannot be produced and processed, the appearance of components is so complex that they cannot be or cannot be produced in other ways. Therefore, it is necessary to find a new high-precision forming and processing technology, so that the wax loss precision casting, which has been widely passed down from ancient times to today, has achieved a crucial development trend in contemporary investment casting through the improvement of raw materials and processing technology. Based on the long-standing new technologies. Therefore, the progress of the aerospace industry has promoted the application of investment casting, and the gradual improvement and enhancement of project investment in precision casting have also created resource advantages for the aerospace industry to further improve its sales performance.
Investment casting is based on ancient wax molds for precision casting. As a civilization with a long history, China was one of the regions that initially applied these new technologies. In the hundreds of years before British Columbia, ancient Chinese laborers developed this type of precision casting technology for precision casting, with various detailed pattern designs. There are also words for watches, clocks, containers and other commodities, such as Zeng Houyi's tomb in the Spring and Autumn Period and the Warring States period. The industrial base of Zeng Guyi Tomb is a pair of intertwined dragons. They are connected head to tail, interleaved from left to right and sequenced to produce a double-layer Weather map in the middle. This pattern design cannot be produced and manufactured according to ordinary precision casting processes. The precision casting process can utilize the objective fact that paraffin has no compressive strength and is easy to carve by hand. With ordinary specialized tools, it can manually carve works of art like lime powder, such as the Yi Tomb of Zeng Kiln. Then, by adding pouring system software, architectural coatings, dewaxing, and pouring, exquisite Zeng Kiln tombs can be obtained.
The characteristic of investment casting is that investment castings have high dimensional precision and surface smoothness, which can reduce production and processing work. However, as long as there is a small amount of machining remaining on the parts, even some castings only have cutting and polishing capacity and can be applied without production processing. It can be seen that investment casting precision casting method can save a lot of mechanical equipment and production time, greatly saving metal materials and raw materials.


What are the advantages and disadvantages of precision casting parts?
Aluminum die castings are widely used in industrial production and can be used as parts of many equipment. The main process used in production is extrusion molding, which has its own advantages and disadvantages and can improve and prevent these defects. Let's talk to the aluminum die-casting manufacturer about the actual information.
Large precision castings use extrusion molding technology, where raw materials such as waste aluminum are melted in a melting furnace and extruded through an extruder to be discharged into the grinding tool for molding. It can also extrude various aluminum profiles with different cross sections. The primary and secondary functions, including compressive strength, strength, and wear resistance, are all in accordance with the standard GB6063. Advantages include: light weight of only 2.8, non rusting, fast overall planning changes, low investment in grinding tools, and vertical extension of over 10 meters. Aluminum alloy profiles have bright and matte appearance, and their treatment process adopts anodic oxidation treatment. The surface treatment oxide film reaches a thickness of 0.12m/m. Gravity casting of aluminum parts and thickness of aluminum alloy profiles are selected based on the optimal control of product planning, not necessarily the thicker the product on the market. The overall planning should be terminated according to the cross-sectional structure regulations, which can vary from 0.5 to 5mm.
The surface quality of aluminum die castings also has relatively difficult to defeat defects: shrinkage, deformation, black stripes, concavities, and a single line. Those with high levels of entrepreneurship and effective overall planning and production process of grinding tools can avoid the occurrence of less significant defects mentioned above. The inspection of defects should be terminated according to the standard inspection method, with a visual angle of 40-50CM to identify the defects.


Market prospects of precision casting manufacturers
The field of stainless steel precision casting is different from the traditional casting industry. Although it is a major foundry country in China, precision casting is still in the development stage and there are still significant differences from developed countries in Europe and America. In recent years, China has vigorously promoted modernization and continuously improved the level of high-tech. There are already some relatively complete methods and methods in precision casting. In addition, the requirements for precision casting products in China are also continuously increasing. Therefore, precision casting, especially stainless steel precision casting, will have extensive indoor space for development in China.
Stainless steel precision casting, also known as sand mold casting precision casting. This machining process tries to avoid or avoid drilling throughout the entire casting process. It is a casting machining process with little or no drilling, and is an excellent production process in the casting industry. It has a particularly wide range of applications, not only suitable for casting various types and metals, but also produces castings with higher specifications, precision, and surface quality than other casting methods. At the same time, for heat-resistant and difficult to produce castings, sand mold casting precision casting method can be used. This type of casting method is more suitable for casting components in high-tech industrial chains such as aerospace, national defense, and security, as it is not subjected to high temperature and high pressure throughout the casting process.
The earliest stainless steel precision casting can be traced back to the 1930s and 1940s. The United States first used stainless steel precision casting to cast turbine blades in its high-tech leading aviation engines at that time, and the finished products received five-star praise in various fields, thus obtaining marketing promotion for this method. The research and application of stainless steel precision casting products in China was established after the founding of the People's Republic of China. With the development of national defense technology in China, stainless steel precision casting research laboratories or foundries have been established in Liaoning, Guizhou, Beijing, Shaanxi, Hunan, and other places. However, objectively speaking, the development of stainless steel precision casting in China is still in its infancy and cannot meet the development requirements in fields such as aerospace and national defense technology.
Due to the high added value of stainless steel precision casting, the field of stainless steel precision casting is different from the traditional casting industry. According to relevant statistical analysis (2013 data information), in the aerospace machinery and excellent automotive engines of European and American countries, the added value of precision casting raw materials accounts for nearly 70% of the total added value, but the domestic market share is less than 35%. Although China is already the country with the largest casting volume, its casting value is still at the upstream level and cannot reach the top-level level. Therefore, the essence and practical significance of developing stainless steel precision casting are the basic requirements for national defense security and technology, and the inevitable choice for economic development.


What factors will affect the accuracy of precision castings?
At present, the global investment casting forming process is developing rapidly and widely used. From the current situation, the future development trend of this process is that casting products are increasingly close to component products, and traditional precision castings are only used as blanks, which is no longer suitable for the rapid changes in the market. The complexity and quality level of component products are increasing, and research and development methods are becoming stronger. Professional collaboration is beginning to emerge, and the application of CAD, CAM, and CAE has become the main technology for component product development. From the current development situation analysis, the application of casting technology is very extensive, and its future development prospects are quite broad.
Today, foundry Dongrong Machinery will have a detailed discussion with you about the factors that affect the accuracy of castings:
In general, the dimensional accuracy of precision castings is influenced by various factors such as casting structure, casting material, mold making, shell making, roasting, pouring, etc. Any unreasonable setting or operation of any link can cause changes in the shrinkage rate of the castings, leading to deviations from the requirements for dimensional accuracy of the castings. The following are the factors that can cause dimensional accuracy defects in precision castings:
(1) The impact of precision casting structure: a. Casting wall thickness, high shrinkage rate, thin casting wall, low shrinkage rate. b. The free shrinkage rate is high, while the hindrance shrinkage rate is low.
(2) The impact of precision casting materials: a. The higher the carbon content in the material, the smaller the linear shrinkage rate. The lower the carbon content, the greater the linear shrinkage rate. b. The casting shrinkage rate of common materials is as follows: casting shrinkage rate K=(LM LJ)/LJ × 99.9%, LM is the cavity size, and LJ is the casting size. K is influenced by the following factors: wax mold K1, casting structure K2, alloy type K3, and pouring temperature K4.
(3) The influence of mold making on the linear shrinkage rate of precision castings: a. The influence of wax injection temperature, wax injection pressure, and pressure holding time on the size of the investment mold is obvious in wax injection temperature, followed by wax injection pressure. The pressure holding time has little effect on the final size of the investment mold Z after ensuring investment molding. b. The linear shrinkage rate of wax (mold) material is about 0.9-1.1%. c. When the mold is stored, further shrinkage will occur, with a shrinkage value of about 10% of the total shrinkage. However, after 12 hours of storage, the size of the mold is basically stable. d. The radial shrinkage rate of wax molds is only 30-40% of the shrinkage rate in the length direction, and the influence of wax injection temperature on the free shrinkage rate is much greater than that on the hindered shrinkage rate (the optimal wax injection temperature is 57-59 ℃, and the higher the temperature, the greater the shrinkage).


What factors will affect the use of precision castings?
How to deal with the problem of electric welding of precision casting parts and how to carry out electric arc welding? As a manufacturer of precision casting parts, let's take you to know!
Taking into account various factors, electric welding and symmetrical welding should be used as much as possible for the welding parts of precision castings, followed by overall welding. This can avoid ground stress causing cracks in precision castings and improve their welding quality.
When welding precision castings, if the joint is relatively small, it is recommended to use 3.2 welding rods. It is not until the second layer is welded by electric welding that 4.0 welding rods are used. Due to the large size of general precision castings, segmented welding can be carried out in 1/6 turns.
For cracks caused during the electric welding process of precision casting manufacturers, they should be cut and welded along both sides of the crack. The deep and long weld seam should be removed from the crack area before re welding. When welding cracks, first seal the stainless steel head and slowly weld along the crack from the root. For those with compressive strength exceeding HRC38, AI02 welding rod shall be used for covering.
The parts of precision castings that must be welded by electric welding in different layers should be cleaned and tidy before welding the second layer when the working temperature of the first layer is cooled to 200-300 ℃. The deduction should be made in sequence, and the next layer of electric welding should not be carried out too hastily to prevent poor welding quality.
When designing heat treatment fixtures, there are always some difficult problems. As a manufacturer of heat treatment fixtures, it is important to pay attention to the common problems that arise when designing heat treatment fixtures. Let's take everyone together to solve them!
1) Conduct a detailed analysis of the product workpiece structure and standard specifications to achieve maximum standards and specifications.
2) Ensure that the work clothes can reliably carry the entire process of heat treatment for goods and workpieces, and have a long service life.
3) Ensure that the transportation of commodity workpieces is evenly heated, high-frequency quenched, carbonitriding, and uniformly cooled on the work clothes.
4) Transport commodity workpieces as much as possible to improve the production efficiency of heat treatment methods and reduce energy consumption.
5) Try to balance the applicability of work clothes as much as possible, reduce the types of work clothes, simplify the management method of chemical factory decoration, and save costs.
6) Minimize work, raw materials, and manufacturing costs as much as possible.


What are the purification skills for precision castings?
The investment casting process contains various residues in the aluminum liquid sucked out by the electrostatic precipitator, so purification is required before casting. In industrial production, purification methods such as clarification, flux, and vapor are mainly used, and some also use fixed solidification and filtration methods for purification.
1. Flux purification: Flux purification is the application of a slimy discharge composed of many fluxes involved in aluminum liquid, allowing the metal oxides in the aluminum liquid to be absorbed and dissolved by this discharge, forming a new discharge that rises to the surface, and after cooling, forms a sludge to be removed. The flux used for purification is composed of salts with low melting point, low relative density, low surface support, high vitality, and strong adsorption on air oxidation slag. When applying, a small piece of flux is first loaded into a cage, and then stabbed into the bottom of the mixing furnace to stir back and forth. Alloy steel precision castings can be cast by removing the cage after the flux is melted, and stopping for 5-10 minutes to remove the surface sludge. According to requirements, the flux can also be removed from the surface to provide a covering effect.
2. Vapor purification gas purification is a major raw aluminum purification method, commonly used as chlorine gas, nitrogen gas, or a mixture of chlorine and nitrogen gas.
(1) Chlorine purification. Previously, active vapor chlorine was used as purifying agent (Chloride process). In the Chloride process process, when chlorine gas enters the aluminum liquid, many abnormally thin AlCl3 and bubbles are formed, which are fully mixed in the aluminum liquid. The hydrogen dissolved in the aluminum liquid, along with some alloy aluminum precision casting equipment impurities, are adsorbed on the AlCl3 bubble, followed by the AlCl3 bubble rising to the surface of the aluminum liquid and discharged. When entering chlorine gas, it can also chlorinate some elements that are more negatively charged than aluminum, such as calcium, sodium, magnesium, etc., which generate corresponding chlorides due to entering chlorine gas and are separated. Therefore, Chloride process is a very effective method for purifying primary aluminum. The amount of chlorine used is 500-700g per ton of aluminum, but because O2 is harmful and precious, in order to avoid gas damage and reduce the cost of waste aluminum production, it has been gradually replaced by Noble gas nitrogen purification method in the contemporary aluminum industry.
(2) Nitrogen purification method. It is also known as the continuous purification method without smoke, using alumina balls (418mm) as the filtering material. N2 immediately enters the aluminum liquid. The aluminum liquid is continuously fed into the purification furnace, passed through the alumina ball filter layer, and subjected to nitrogen flushing. Therefore, the non-metallic material impurities and their dissolved hydrogen in the aluminum liquid are removed, and then continuously discharged, resulting in even distribution of slender nitrogen bubbles in the solved aluminum liquid, which has purification effect. Nitrogen has zero air pollution and a large purification output, which can solve 200-600kg of aluminum liquid per minute. The amount of aluminum loss generated during the entire purification process is relatively reduced, so it is now widely used. But unlike chlorine gas, it can remove calcium, sodium, and magnesium from aluminum liquid.


What is the difference between general castings and precision castings?
Precision castings are different from general castings:
Precision casting is the process of pouring liquid metal water concrete into the same solid mold as the casting, and cooling it to form the casting. The casting methods include sand mold casting, special casting, precision casting, and precision casting in V precision casting, which are divided into special casting. The parts cast using this method do not require production processing and may require minimal production processing.
Generally speaking, casting is a superficial form of forging, while aluminum die casting is a casting method of working pressure casting. Under high-pressure conditions, liquid metal materials are added to the casting physical model at a higher rate. Condensation under working pressure. Generally speaking, casting has multiple materials and external forces that deform under condensation conditions. Precision casting and general casting are two different casting methods, but precision casting has higher regulations and stronger accuracy. Compared with traditional sand mold casting processes, precision casting produces larger castings with stronger surface smoothness. Including: investment casting, ceramic mold casting, metal material mold casting, working pressure casting, and lost foam casting. The overall surface coating of stainless steel precision castings determines the process performance of the castings. Therefore, it is stipulated that the coating quality is high, the silica powder is fine, the coating viscosity should not be too high, and the sand removal should also be fine. Structural reinforcement coatings can improve the effectiveness of the shell and avoid damage to the shell. Therefore, thicker silica powder can be used, the paint viscosity is high, and the Degree distribution of desanding particles is also large.


What factors will affect the quality of precision castings?
Through experiments, it can be seen that hydrochloric acid oxide film is a key factor that endangers the purity and clarity of the oxide film on stainless steel precision castings. Its thickness, porosity, purity, and grouting reinforcement quality all immediately affect the mirror effect of the casting. If there are many impurities in the oxide film, its purity will decrease, and the clarity of the cylinder section will be reduced.
Therefore, to ensure the actual effect of mirror treatment on stainless steel plate precision castings, it is necessary to reduce the impurity content in the oxide film. Therefore, it is necessary to effectively control the thickness, porosity, purity, and sealing quality of plastic films, so as not to affect production and processing as much as possible.
The impurities in the oxide film mainly come from the stainless steel plate precision casting itself, and a part comes from the oxidation bath. Therefore, moderately reducing the content of alloy elements in precision casting parts can greatly reduce the impurity content. At the same time, reducing the impurities and cations in the tank liquid, maintaining the freshness of the tank liquid, can also improve the purity of the oxide film.
From this, it can be seen that the mirror treatment processing process of stainless steel plate precision castings cannot be successfully completed. To achieve good results, it is necessary to remove various influencing factors, so that the processing technology can fully exert its excellent effects, and the quality of all stainless steel precision castings will also be correspondingly improved.


What are the causes of cracks in precision castings?
Stainless steel precision castings are a useful production process in steel enterprises, widely used, and can be cast in various types and aluminum. So, what is your suggestion for cracks in stainless steel precision castings?
The suggestions for cracking in stainless steel precision castings are shown below:
1. Heating, when dealing with defects in stainless steel plate castings, should adhere to heating standards. During the entire process of blowing welding, the product workpiece should be heated to above 108 ℃.
2. In the smelting process, minimize the composition of harmful elements such as P.S, and reduce the composition of gases such as N.H.O and dirt as much as possible. Low phosphorus steel intermediate aluminum alloy profiles can produce good results.
3. Thermal insulation: According to the appropriate increase in the thermal insulation time of sand castings, it is important to control the unpacking working temperature to be less than 70 ℃, ensure that the sand castings are fully packed with liquid and solid materials, and avoid internal stress caused by external forces.
4. When sand falls, it is strictly prohibited to irrigate the sand mold and castings during the sand removal step of the casting. It is strictly prohibited to use strong external forces such as box collision to cause destructive sand falls, and to avoid the mutual influence of external forces and internal stress of the casting, causing cracks.
5. Fiber laser cutting of the glue inlet, select the appropriate process for making the sincere pouring glue inlet according to the casting specifications, and ensure that the sincere working temperature is not less than 300 ℃.
6. For the structure of stainless steel plate castings, comprehensive consideration should be given to factors that can damage the liquid and solid collapse of the castings during the entire forging process, such as pattern, large thickness, and docking. Choose appropriate technical basic parameters to prevent defects, such as folding and folding.
Stainless steel forging.
When cracks occur in high-precision stainless steel castings, we can follow the above operation process and apply our castings.


Previous page
1
2
Next page
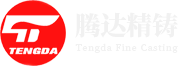

Tel
0595 - 22651212

Adress
No.126 Houcheng, Wuzhai Village, Heshi Town, Luojiang District, Quanzhou City, Fujian Province
ABOUT US
NEWS
CONTACT
Page copyright Quanzhou Tengda Fine Casting Co.,Ltd.